Story and photos by Brady Creel '03
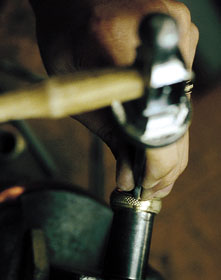
Photo by Brady Creel '03
Making an Aggie Ring is not unlike wearing one:
Not just anybody can do it.
At Balfour, the company that has manufactured Aggie Rings since 1947, the best 12 of 400 jewelers make the Aggie Rings. It’s the most prestigious job in the plant. Working on the "Aggie Ring line" is a privilege earned over time, granted only to the most talented craftsmen.
"It’s the place to be," said David Collier, Balfour’s director of manufacturing.
This is Balfour’s "key-accounts" group - where the company’s best jewelers work on Balfour’s most prestigious accounts, making rings for Baylor University, the U.S. Military Academy at West Point, Notre Dame and the New York Yankees.
Balfour makes more than 15,000 Aggie Rings every year - more than three times as many as Clemson, A&M’s closest competitor. For the key-accounts jewelers, Aggie Rings take first chair, and no piece of jewelry in the plant gets as much attention.
In the team’s work room near the center of Balfour’s plant, a banner- complete with a block "aTm" at either end - boasts the 12 jewelers’ 273 combined years of experience. They know their craft well and take great pride in it.
"As proud as you are to wear the Ring, our jewelers are as proud to make them," said Harold Leverett, Balfour’s college marketing project manager. "They know what it means to be an Aggie."
Breaking the Mold
Balfour uses a lost-wax induction process to make Aggie Rings, a process that has been in place since sometime in the 1960s. By this process, every Aggie Ring is first made in wax - size 6 for ladies or size 10 for men. This is because Balfour’s masters - the brass originals from which all Aggie Rings have been cast since the process was adopted-are engraved as sizes 6 and 10. These masters are used to forge the metal molds which, in turn, are used to make wax injections of the rings.
Silvia Mireles performs the first step in the meticulous process by which each Aggie Ring is made. She makes the wax injections - wax replicas of Aggie Rings - that are later used to create molds. In her years at Balfour, she has made about 70,000 of them.
"I’ve made a lot of rings," Mireles said. "I even dream about them." After Mireles makes the wax rings, Minga Garcia resizes each wax ring and trims away any excess. For smaller rings, Garcia cuts away the excess wax; for larger ones, she adds wax to fill in the gap.
After the wax rings are made, resized and trimmed, they are passed to "tree-up," where they are clustered onto a "ring tree." From there, the wax trees go to investing where they are prepared for "burn-out."
In this phase, investment powder is mixed with water in a very precise ratio. The mixture is poured around the wax trees and allowed to solidify. Then it goes to casting, and the mold is baked overnight at 1,300 degrees. Slowly, the wax tree melts away and the mold hardens, leaving a hollow, negative facsimile of the rings inside.
Next, in the casting room, Richard Rodriguez weighs out enough gold to make the number of rings in each tree and pours the gold pellets into a production casting machine. Cautiously, he puts the hot mold in the bottom of the casting machine, which heats the gold to about 1,800 degrees and drops the molten metal into the mold. From the bottom up, the gold fills the hollow chamber, creating a gold tree of Aggie Rings. Rodriguez removes the mold, complete with blazing gold, and sets it aside to cool.
After the gold has cooled, Rodriguez and his team "knock out" the mold. Simply put, they use water and tools to remove the hardened investment powder from the gold tree. When the investment powder is gone and the tree is all that remains, Rodriguez sandblasts the tree and then uses powered bolt cutters to remove each Aggie Ring.
One Ring at a Time
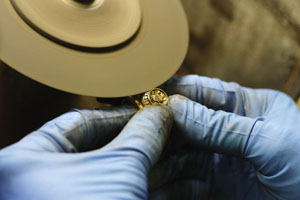
Photo by Brady Creel '03
The Rings come off the tree with little luster or shine. They appear crude, almost unfamiliar. Then, the skilled craftsmen of the Aggie Ring line take over. Each jeweler has a specific finishing task, be it polishing the shield or carving the star.
First, the sprue, the piece of gold that attaches the Ring to the tree, is ground off, leaving a smooth palm side. Then, the familiar dimples, or pebbling, are hand engraved on each Ring by one of three Balfour jewelers - Joe, Mingo or Bill. With skilled hands, they quickly engrave the dimples.
"They can pick up a ring and tell you who put the pebbling in," Collier said. "It’s like a signature - they leave something behind."
After the pebbles are engraved, the Rings are antiqued. All Rings - dark, rose or natural finish - are antiqued, but the process is different for each finish. The dark Rings come out of antiquing solid black and barely recognizable; those with rose and natural finishes have a similarly deceiving look, though not as dark. With great care and craftsmanship, Balfour’s best painstakingly polish every detail of each Aggie Ring.
Raquel Lopez, who is responsible for quality control on the Aggie Ring line, makes sure the Rings are perfect. She has an Association of Former Students poster near her desk featuring a picture of a 1982 Aggie Ring and the words "The Ring is the thing." On her desk is an envelope that says "aTm, please rush." Lopez is efficient but she doesn’t get in a hurry.
"After 22 years of checking Rings, you know what to look for," Collier said of Lopez,who has never scored less than 100 percent on her quality-control audits. If there is something wrong, she sends it back. "I say ‘Fix it,’" Lopez said. "I want it right."
Aggie Ties that Bind
Former students, Aggie parents and friends of A&M are among the people that make up the Aggie Network. And the Aggie Network is alive and well at Balfour.
Mike Goodwin ’85 is the keeper of the Aggie Ring masters. As Balfour’s manager of master tooling and engineering, he is responsible for protecting the two sets of hand-engraved originals - one men’s, one women’s - that have been used to make every Aggie Ring since some time in the 1960s.
In the shipping department, Connie Miller, an Aggie mom to Kimberly Cottrell ’00, makes sure the Aggie Rings are shipped out as promised and that Aggie Ring repairs are handled with special care.
Special attention is paid to the Aggie Ring throughout Balfour, so when David Collier saw an opportunity to make the ring even better, he did. When Balfour’s ring production plant was moved from Massachusetts to Texas in 1997, Collier took over as Balfour’s director of manufacturing, and began to examine the process by which Aggie Rings were made.
Previously, all Aggie Rings were constructed from two pieces: the shanks and underside were cast separately from the base, the rope-trimmed top that contains the class year. Collier and his team reengineered the process so they could make Rings of a single solid piece of metal. "I said, ‘Why make a two-piece Ring?’ "Collier said of the change. "It’s been a better-quality product since then."
And Collier has a good reason to be so concerned about the Aggie Rings. His wife, Lana, is Fightin' Texas Aggie Class of 1978. "This guy makes a million rings a year," Leverett said, "and every morning when he leaves for work, his wife says, 'Look after the Aggie Rings.'"
With true Aggie pride, he does.